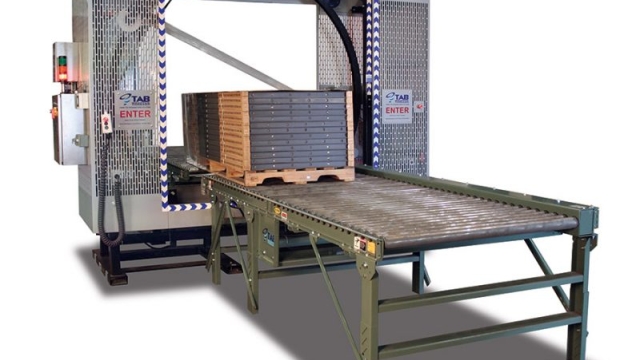
Revolutionizing Packaging Efficiency: The Ultimate Guide to Pallet Wrappers, Stretch Wrappers, and Stretch Wrap Machines
Packaging efficiency plays a crucial role in today’s fast-paced business environment. Companies across various industries rely on pallet wrappers, stretch wrappers, and stretch wrap machines to streamline their packaging processes and optimize productivity. These innovative tools have revolutionized how goods are prepared for transportation and storage, ensuring that products are securely wrapped and protected during transit.
A pallet wrapper, also known as a pallet wrapping machine, is specifically designed to securely wrap palletized goods with stretch film. By encasing the entire pallet load with stretch film, a pallet wrapper ensures that the products remain intact and stable during transportation. This not only prevents items from shifting or falling off the pallet but also minimizes the risk of damage or breakage, ultimately protecting both the goods and the company’s bottom line.

Similarly, a stretch wrapper is a versatile machine used to wrap various types of loads, from individual products to smaller stacks of goods. It utilizes stretch film to tightly hold and secure the load, providing stability and protection against moisture, dust, and other external factors. These machines are especially valuable in industries where goods need to be stored or transported in bulk, as they significantly enhance efficiency and minimize the risk of damage or loss.
A stretch wrap machine takes packaging efficiency to the next level by automating the entire wrapping process. These machines are designed to handle high volumes of packaging, reducing labor costs and ensuring consistent, uniform wrap tension. With adjustable settings and advanced features like pre-stretch capabilities, a stretch wrap machine can be tailored to meet the unique packaging requirements of different industries and load types.
In the following sections, we will explore the key features, benefits, and considerations when selecting pallet wrappers, stretch wrappers, and stretch wrap machines. By understanding the ins and outs of these packaging tools, businesses can make informed decisions that will revolutionize their packaging efficiency and ultimately contribute to their overall success.
Understanding the Basics of Pallet Wrappers
Pallet wrappers are powerful machines that streamline the packaging process by securely enclosing palletized loads with stretch wrap. By automating this task, businesses can achieve significant time and cost savings while ensuring the stability and protection of their products during transportation and storage.
A pallet wrapper, also known as a stretch wrapper or stretch wrap machine, utilizes a roll of stretch film to tightly bind the load together. The machine typically consists of a turntable on which the pallet rotates, a film carriage that wraps the stretch film around the load, and various controls for adjusting wrapping speed, tension, and other settings.
Pallet Wrapping Machine
When operating a pallet wrapper, the load is positioned on the turntable, and the desired amount of stretch film is pulled from the roll. As the turntable rotates, the film carriage moves up and down, creating a spiral pattern that securely encompasses the load in layers of stretch wrap. The tension of the film can be adjusted to optimize stability while preventing damage to the products.
There are different types of pallet wrappers available, including semi-automatic and fully automatic models. Semi-automatic pallet wrappers require manual interaction to attach the stretch film to the load, while fully automatic machines perform all functions without any operator intervention. Both types come with their own advantages and can be selected based on the specific needs and volume of packaging required.
Understanding the basics of pallet wrappers is crucial for businesses looking to revolutionize their packaging efficiency. By investing in the right machine and mastering its operation, companies can enhance the protection and stability of their products while making significant strides in optimizing their packaging processes.
Exploring the Different Types of Stretch Wrap Machines
In the world of packaging efficiency, stretch wrap machines play a crucial role in securing and protecting goods during transit. These machines revolutionize the way pallets are wrapped, providing a reliable and consistent method that saves time and reduces costs.
Pallet Wrapper:
One popular type of stretch wrap machine is the pallet wrapper. This machine is specifically designed to wrap the stretch film around palletized goods. It automates the wrapping process, ensuring that the film is tightly secured around the pallet, providing stability and protection. Pallet wrappers can be categorized into different types based on their operation, such as turntable wrappers, rotary arm wrappers, and orbital wrappers. Each type offers unique benefits depending on the specific requirements of the packaging operation.
Stretch Wapper:
Another type of stretch wrap machine is the stretch wapper. Similar to the pallet wrapper, the stretch wapper is used to wrap stretch film around goods for shipping and storage purposes. The main difference is that the stretch wapper is more versatile, allowing it to handle various package shapes and sizes. This flexibility makes it an ideal choice for businesses that deal with different types of products and packaging configurations.
Stretch Wrap Machine:
Lastly, we have the stretch wrap machine, which encompasses both the pallet wrapper and the stretch wapper. These machines are designed to automate the process of stretching and wrapping film around items, providing increased efficiency and consistency. With advanced features such as pre-stretching mechanisms and adjustable tension controls, stretch wrap machines offer superior wrapping techniques that ensure the stability and protection of goods throughout the supply chain.
By understanding the different types of stretch wrap machines available, businesses can make informed decisions about which machine best suits their packaging needs. Implementing the right stretch wrap machine can bring significant improvements in packaging efficiency, cost reduction, and product integrity.
Maximizing Efficiency: Tips and Best Practices when Using Pallet Wrappers
Proper Machine Selection:
Choosing the right pallet wrapping machine is crucial for maximizing efficiency. Consider factors such as the size and weight of your pallets, the desired level of load stability, and the volume of pallets to be wrapped. Opting for a machine with adjustable settings and customizable options will allow you to adapt to varying requirements easily.Optimize Film Usage:
Stretch wrap film is a valuable resource that should be utilized efficiently. By ensuring proper tension and stretch applied during the wrapping process, you can reduce the amount of film used while maintaining load stability. Additionally, selecting the appropriate film gauge for your specific application can help minimize waste and save costs in the long run.Prioritize Load Stability:
The primary goal of pallet wrapping is to secure the load in place during transportation and storage. To achieve optimal load stability, make sure to use enough revolutions of stretch wrap around the pallet. Pay attention to the bottom layers of the load as they play a critical role in preventing shifting and toppling. Considering the specific characteristics of your products and matching them with suitable wrapping techniques can significantly enhance load security.
Remember, by taking these tips and best practices into account, you can revolutionize your packaging efficiency and maximize the benefits gained from pallet wrappers, stretch wrappers, and stretch wrap machines.